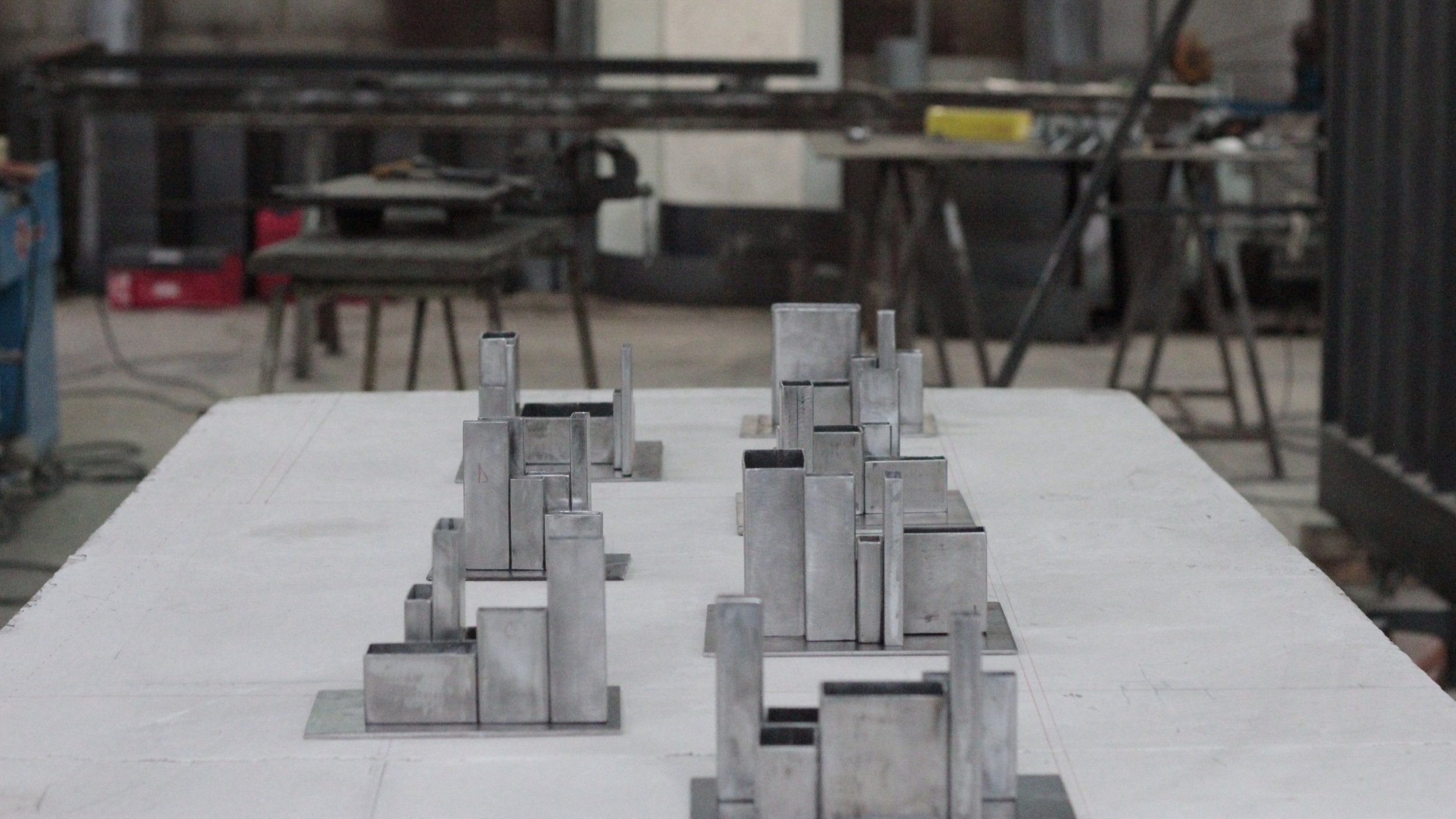
A New Design Craft project bridging traditional blacksmithing and generative coding.
Generative craft.
The Why
In an age of automation and mass production, traditional blacksmithing risks becoming a lost craft.
Once deeply embedded in local economies and material cultures, blacksmithing is now largely replaced by industrial manufacturing.
But what if technology could revitalise, rather than replace, heritage craftsmanship?
Generative Craft originated from reflections on this challenge. blending traditional forging techniques with generative programming, it explores a new paradigm where tradition and innovation co-create rather than compete.
Hi! I am elia, a designer and design researcher.
with new design craft, I investigated a post-industrial design paradigm for the revitalisation of local identities and community empowerment.
generative crafts is a vital part of my research.
The concept
Can a hammer and an algorithm cooperate towards a shared vision?
This is the question I wanted to try and answer with Generative Craft. In the age of Artificial Intelligence, as a designer I was fascinated by the possibility of merging Artisanal Intelligence and computational design, using generative programming (Processing) to create ever-evolving patterns that inform the forming process while still keeping the control over the output in the hands of the humans involved in the process.
To me, Artisanal Intelligence sits on the opposite side of the spectrum in comparison to AI: unlike its artificial counterpart, Artisanal Intelligence is extremely human. It doesn’t think in terms of pre-made frameworks and schemata but it increases its knowledge organically through direct experience.
So, instead of rigid, predefined templates, the algorithm suggests forms that become collaboration tools between the designer and the blacksmith who, ultimately, interprets and adapts these inputs in real-time with their hands and intuition. This collaboration between human craftsmanship and machines is coordinated by the designer's ability to facilitate processes of knowledge exchange.
The artisans.
This project celebrates the artisanal expertise and the cultural openness of Carlo and Gianluca Guttilla, the last of a family of blacksmiths with over three generations of experience in blacksmithing.
Known for his dedication to traditional techniques mixed with a love for free experimental expression, Carlo Guttilla has spent decades perfecting the balance between precision and creativity. Today Carlo runs his workshop together with his sons, especially his youngest Gianluca, a properly adept right-hand man.
The workshop, dated 1930, is located in Lercara Friddi, a small town in the Sicilian hinterland where it remains as one of the rare traces of an artisanal past. Here Carlo came back when he was in his 30s after years spent wandering abroad across Australia and Northern Europe looking for a place where his creative vision of blacksmithing could find fertile soil and his creative language could blossom.
the workshop
CARLO GUTTILLA
gianluca GUTTILLA
“in my years abroad, I never felt like an emigrant, but rather a minstrel, who instead of playing the guitar, carried around the art of ironworking”
— Carlo Guttilla
The Process
-
1. Mapping of Metal Scraps
The first step involved analysing and mapping leftover metal scraps from previous blacksmithing production. By cataloguing these materials, I identified existing geometries and structural conditions that were used for the generative step of the process. Rather than discarding excess material, I incorporated it into a new workflow.
-
2. Building the Algorithm
Using Processing, I developed a generative algorithm that creates non-repetitive patterns based on the mapped geometries. Each iteration produced adaptive blueprints responding to the available metal profiles without dictating fixed designs but acting as a generative collaborative tool to explore new languages.
-
3. Blueprint Selection
From over 100 algorithmically generated patterns, I curated and selected the most viable blueprints for forging. This selection was based on key criteria, including material constraints, structural feasibility, and aesthetic value. The goal was to ensure that the design was respectful of the mechanical limitations of the reclaimed metal.
-
4. Metal Cutting & Preparation
Before the forging process begins, the selected metal pieces undergo cutting and shaping to align with the computational patterns. Traditional tools —such as water-cutters and milling machines— are employed to extract the forms while preserving the inherent qualities of the reclaimed metal. This step ensures that each piece is prepared for forging.
-
5.Hand-Forging & Welding
The generative blueprint served as a guiding principle, but the physicality of metalworking dictated the final outcome. The blacksmith interprets the computational design through heat, hammering, and welding, reinforcing the co-creation process between the algorithm and the artisan.
-
6. Refinement & Finishing
Each piece undergoes traditional blacksmithing finishing techniques, such as brushing, oiling, and polishing, to preserve the raw aesthetic of handcrafted metalwork. The result is a small series of eight unique, technical pieces that retain both the organic marks of blacksmithing and the structural accuracy of computational design.
Process And results